How to Drill a Hole in a Long Dowel
I am managing a task that involves a longitudinally guiding of a thru-hole via a dowel. (The corresponding pipe has been used as a cam cap for my wood camshaft.) I needed to do some of those, and the methods I learned online weren’t working well enough for me. Here is my post, in 3 easy stages, demonstrating how works for myself.
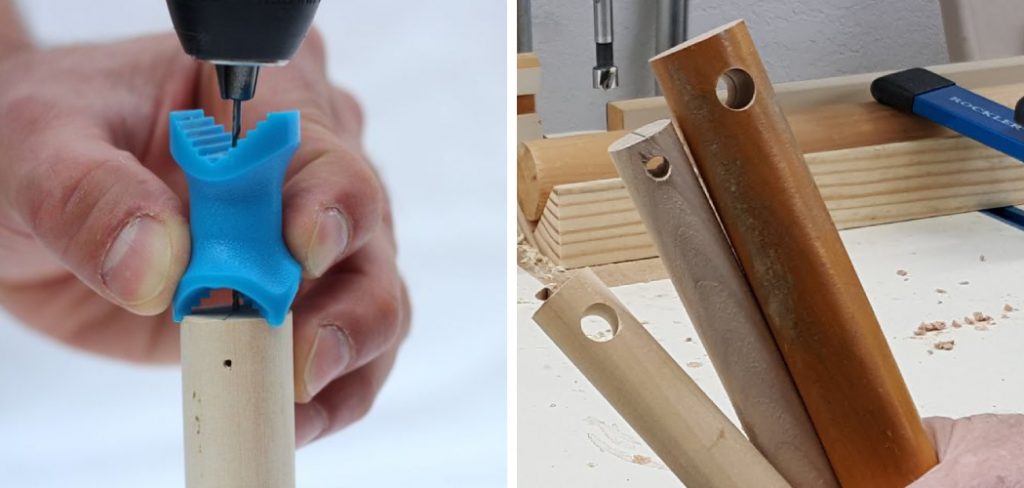
Instructions:
Type 1:
Grab a slice of wooden pallets, then cut a hole in a dowel’s side a few more inches apart from one edge. (3/4 inch in my scenario.) To assure that the void is made perpendicular, choose a power drill, when appropriate.
See a space around 1/4 “deep of one edge of the field to the other. (I would use a tabletop saw to use it.) Label your dowel’s center-point. (There have been some excellent clips on how to locate a dowel’s centerpiece.) Choose a punch to mark the centerpiece; this will help lead the power drill over the next stage. To make your dowel more creative, try using a different punch to mark the center-point.
You will need a dowel and a drill bit. The dowel will fit into the drill bit and will be a little loose, so you will need to put in some fasteners to improve the fit. Place the jig on the edge of a piece of wood and lock it onto the drilling machine board. Cover the drill bit’s middle line with the bit. I’m using just a 25/64ths piece, so I would like the dowel openings to cozily accommodate a 3/8 “dowel yet flexible enough to move the dowel.
Perhaps it is using another clamp to pull the “jaws” from the fixture – the hands-on side of the opening. This helps to hold the dowel in the jig tightly, so it won’t rotate until you begin to dig. Dig out the gap. The jig catches the dowel at ninety degrees and does not turn.
Via the dowel’s duration, you will finish up with a perfectly formed gap. This fits well with locknuts, stopping harnesses and cam collars for animation or running plays and every other example wherever you want a specific “tube” of woods.
Finally, put away your common, mass-produced twist drill bits and invest instead in quality carpentry bits like brad-point or Forstner bits. As you’ll see, these twist bits lack the precision and specificity needed for these two options. They are also more likely to damage the workpiece.
We choose brad-point pieces up to 1⁄2 “and Forstner parts (in some packs up to 4”) for more generous dimensions. Since Forstner pieces are driven by the edge rather than the centerline, they will not wander off course when they maintain contact with the wood.
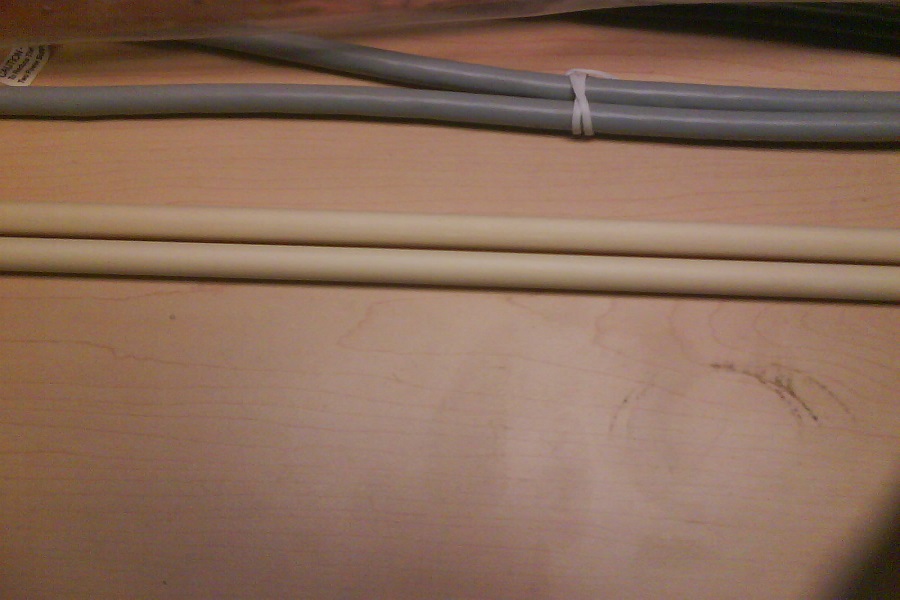
Type 2:
I create a small, efficient method that functions well, especially with a portable corded or wireless drill fastened to a wooden board. The void for such a venture is 1/8 “in size, but often I use levels ranging around 1/16,” 1/8 “to 3/16” in duration from 10 to 16 in. I purchased a 6 inches bit from every diameter and a 12 inches bit. The piece needs to be straight without even a bow or bend because it can drill accurately.
Typically this isn’t a concern with the height of 6 inches but is a widespread issue with a length of 12 inches. Until I noticed the fair bit, I would have to do three shop swaps. The configuration of the drill bit is quick and straightforward to mount and bring down. I began with a portion of plywood about 16 in by 30 in which I had spread around for the foundation, but that scale is random and larger than really needed, so pick a scale that fits your requirements.
I tightened it to a tiny desk that was 2 feet by 4 feet. I placed a wireless drill sideways for this task and fastened to the hardboard for stabilization with 2 “x 2” x 8 “wooden blocks on every line. Then, such blocks are tightened to the board. Monitor the condition from both sides and make changes wherever appropriate.
Note that the fasteners are not just installed for better reliability, nor can also be possible without unplugging the process to enable the drilling battery ever to be adjusted. Using a channel is essential to direct the dowel that you are drilling. It may be achieved by either carving a “v” on the tabletop saw in a wood section or through other equivalent methods.
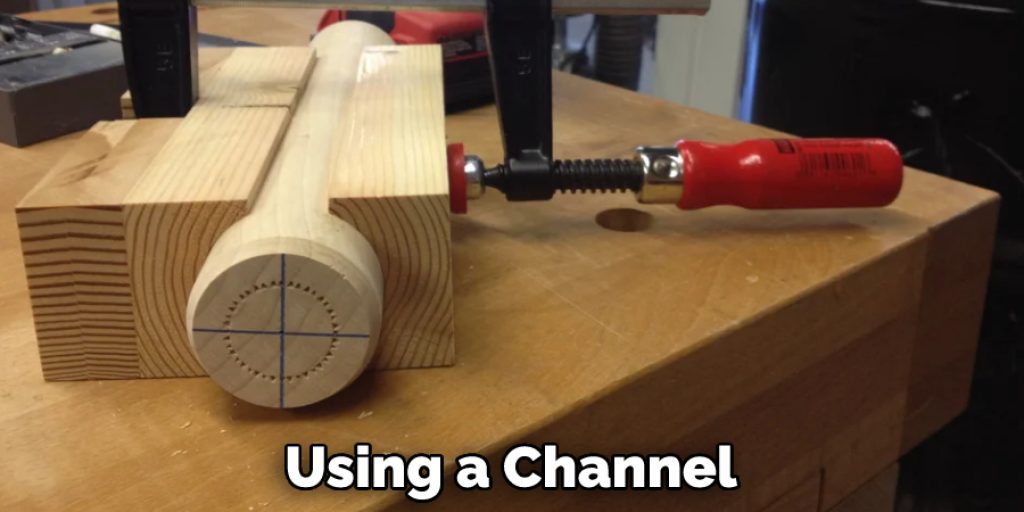
I managed to get a bullnose or step nose stock too long, remaining over to a hardwood flooring job. The bullnose was being used to complete the timber, in which the stairs were connected. I attached the bullnose sideways on a 6 “x 3⁄4” x 2 “long frame. I then fastened the 6” frame onto the plywood at the level needed regarding
the power drill.
The dowel middle could be the same size and parallel to the power drill, so you will need to use several tiny fasteners to align it. I have had to create a few small changes to fit correctly with the pins supporting the frame. Now I’m able to cut a 1/8 “void into a 14 inches long piece of plywood. Next, the middle point was calculated on both sides of the dowel.
I wanted to use a narrower 1/16 “bit a few ways with intentions to turn to a 1/8” bit to widen the gap, hoping it could simplify things. This turned out to be a terrible idea because when I moved to the 1/8 “bit, it emerged via the dowel edge until hitting the rim. I propose that you begin and end by the exact size you want to hole.
I started punching around 3 in length that used a standard 1/8 “drill bit to have the gap started straight as an arrow. Well, I shifted to the 6-inch drill bit, keeping my better to leave being off route. When I come to the end of the 6-inches bit, I moved over to a 12-inch bit.
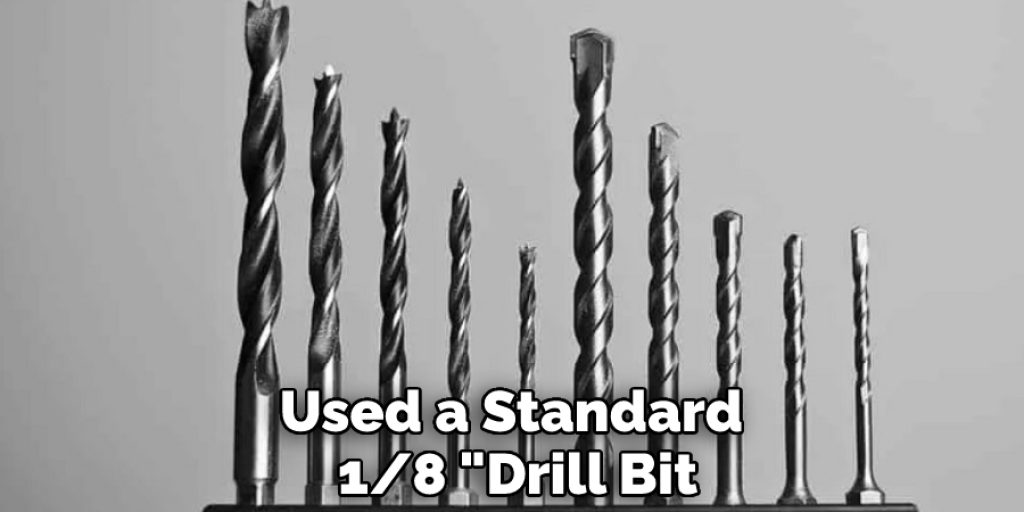
Become careful and watch the distance and be careful you’re always parallel to the piece and inventory. Give it your best shot, and be sure to go out periodically and clean the sawdust off. It might be beneficial or even appropriate to test with arrangements and reach in the middle at either finishing off the dowel based on the dowel duration.
You May Read Also.