How to Increase CFM on Air Compressor
An air compressor is an essential tool for any shop or garage. It’s used to power tools that require air, especially pneumatic ones. However, some compressors cannot produce enough CFM (cubic feet per minute) of airflow through the hose and into your tools.
If you’re having trouble with getting enough pressure at the end of your hose, there are a few things you can do to fix it without buying a new compressor or spending hours tinkering with it yourself. These blog posts will show you how to increase Cfm on air compressors. So read on to find out the techniques.
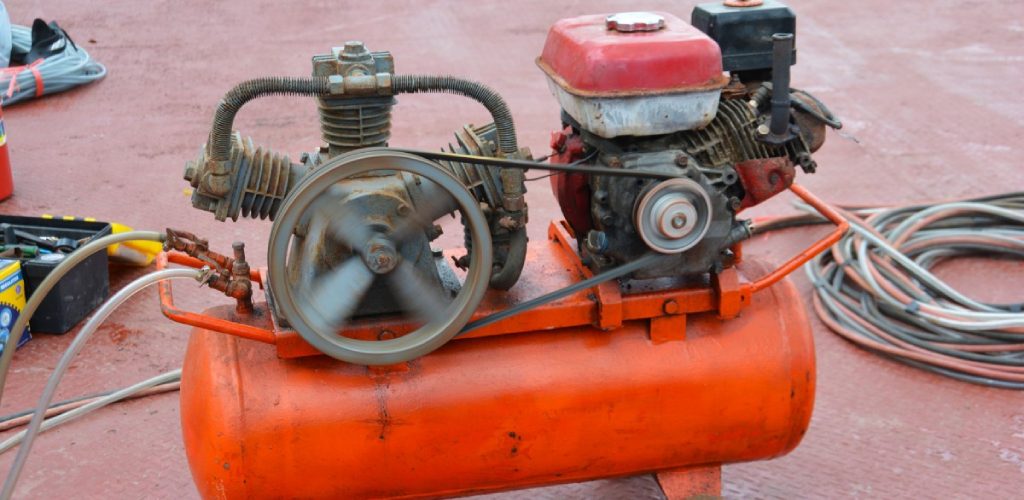
10 Reasons Why You Should Increase CFM on Air Compressor:
1) The life of your tools and equipment will increase with the increased CFM.
2) For every 1 PSI lost due to a decrease in CFM, about 2.5 HP (horsepower) is wasted.
3) With higher CFM, you can handle more workload without waiting for the compressor to catch up.
4) You will not have to buy an expensive, high CFM compressor.
5) The compressor’s life will be longer with higher CFM and HP (horsepower).
6) With higher CFM, you can work more efficiently and get the job done faster.
7) Higher CFM and HP (horsepower) will reduce the amount of noise your compressor makes.
8) You can reach higher working heights without sacrificing CFM or HP (horsepower).
9) With better CFM, you will work longer hours with less wear and tear on the equipment at a lower cost.
10) Higher CFM and HP (horsepower) reduce the number of times you need to turn off and on your compressor.
15 Simple Methods on How to Increase CFM on Air Compressor:
1. Replace The Air Filter:
Clean or replace your air cleaner to keep your pneumatic tools and equipment running smoothly. Clean filters are essential for proper airflow and increased CFM (Cubic Feet per Minute). Some manufacturers recommend changing the filter every 25 hours of use, while others say you should change out dirty filters when they become clogged.
2. Check Air Hoses:
Loose or damaged air hoses can cause an inadequate compressed air supply, reducing the output of CFM (cubic feet per minute). Inspect all your air hoses each time you use them to ensure no nicks, cuts, cracks, or other damage to the hose. If there is any damage, the hose should be replaced.
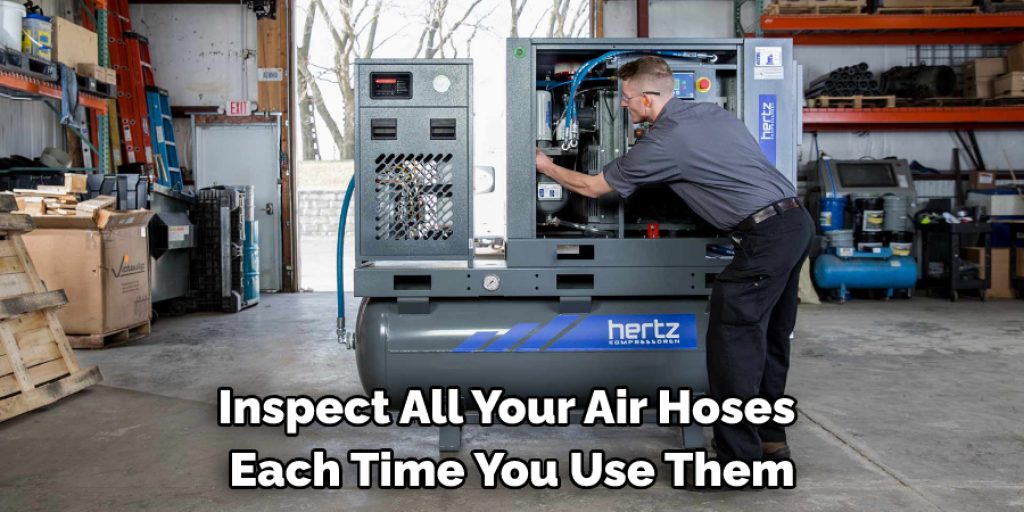
3. Tune-Up Your Compressor:
According to the manufacturer’s instructions, keeping your air compressor running at peak efficiency ensures it’s properly tuned up and lubricated. Many manufacturers recommend maintenance procedures that include cleaning or replacing certain valves or filters that require periodic attention. So whether you’re just a weekend warrior or a seasoned professional, have your compressor tuned up by an authorized factory technician.
4. Use The Proper Hose:
Your air hose is the lifeline between you and your equipment. Always use an approved air hose to connect your pneumatic tools and equipment to the compressed air supply through the designated coupler. Air hoses must resist abrasion and contain a wire helix for reinforcement.
5. Use The Proper Air Tool:
When you use the appropriate air tool, it helps maintain system efficiency. Specialty air tools will increase the productivity of compressed air applications when used for their intended purpose. Ensure your pneumatic tool works well to get the most out of your compressed air system.
6. Check Out The Piping:
The piping between your compressor and tools should be made of metal tubing or a flexible hose. Ensure the fittings are suitable for use with compressed air and no leaks in the pipe or joints. Tighten any loose fittings to ensure there are no air leaks.
7. Keep it Clean:
Clean your tools after each use so they will run better next time. This includes the outside of pneumatic tools, as well as internal parts. Use compressed air to blow out any dust or debris before using the tool again. This will keep your equipment running better and increase your CFM.
8. Keep Out Of The Heat:
Compressed air will release moisture when exposed to high temperatures, reducing the efficiency of any pneumatic tool or equipment. Make sure you’re using an approved air hose that is resistant to hot and cold temperatures or a stainless steel braided hose when working in extreme temperature conditions.
9. Repair Leaks In System:
Leaks in your compressed air system will cause a dramatic decrease in the CFM (cubic feet per minute) output. These leaks can be caused by loose connections, bad couplers, or damaged hoses. If you have any leaks, they should be repaired immediately to prevent further damage and increased costs.
10. Get Rid Of That Air Cap:
Many pneumatic tools and equipment will have an air cap. This is used to prevent moisture from entering the tool while it’s not in use, but this also restricts airflow, reducing CFM (Cubic Feet per Minute). If you remove the air cap before using your tool, you can expect increased performance from your tools and equipment.

11. Service Your Tool:
Most air tool manufacturers recommend servicing your tools every so often, depending on how much you use them. This can ensure maximum CFM (Cubic Feet per Minute) and performance from your pneumatic tools and equipment, and this will also reduce the risk of accidents occurring while using your equipment.
12. Check Cylinder Bore For Scoring Or Pitting:
Scoring or pitting in the cylinder bore of an automatic lubricator can restrict the flow of lubricant. Therefore, these bores need to be free of scoring, pits, and corrosion to ensure smooth movement of the plunger for optimum performance.
13. Lubricate Your Equipment:
Air tools must incorporate elements that require lubrication (bearings, valves, valve seats) to avoid damage. Keeping your pneumatic tools and equipment lubricated will ensure the smooth operation of the various elements throughout the tool’s life.
14. Check The Filter:
Make sure you have a clean air filter on any pneumatic tool or equipment that requires one. A clogged filter restricts airflow, which will decrease your tools’ CFM (Cubic Feet per Minute) output.
15. Keep Out Of The Dirt:
Keeping pneumatic tools and equipment clean can also improve their performance. Ensure you’re using the appropriate air hose for dusty, dirty, or other tough work environments to prevent potential problems with air leakage. When operating in harsh conditions, it may be necessary to use a filter dryer and a filter to remove moisture and other contaminants.
You Can Check It Out to Adjust Torque on Air Impact Wrench
Tips and Suggestions:
Here we have given some tips and suggestions on increasing cfm on the air compressor.
1. Check for blockages in the compressor, which can reduce airflow. This will be done by removing any hoses between components and testing airflow through them. If there is no obstruction, it could be that the compressor is underpowered to begin with, or you are using too many tools that require an air hose at once.
2. If the compressor is not underpowered, then a system component may have been damaged or obstructed in some way.
3. Check to ensure there are no cracks in any components of your air tank, which can also reduce airflow and overall system performance.
4. Another thing to check is your system’s pressure switch. If this has become dirty or unadjusted, it can prevent the compressor from turning on when needed.

5. Check your fittings to ensure that they are tight and not allowing compressor air to escape.
6. Make sure that your filters are clean and fully functional, which is critical if you are going to use an air compressor for things like sanding or other dust-intense activities.
Precautions and Safety Measures:
1. Before doing anything on your air compressor, ensure it is unplugged or turned off any switches.
2. If you are using a compressor tank that has been sitting for a long time, then be sure to let it sit and “recover” for approximately 8 hours after unplugging it. This process is necessary to get rid of any moisture in the tank.
3. Make sure there isn’t anything blocking the intake or outlet of the compressor.
4. Make sure to wear safety equipment, such as glasses and gloves, when working around machinery to prevent any injuries.
5. Be mindful of sharp edges on the tanks.
6. Some parts of the compressor may be under pressure, so make sure you know where all valves are and how to turn them off in an emergency.
7. If you don’t have access to compressed air for your project, try using a different approach to get the job done or find another method.
Conclusion:
To increase CFM, several steps can be taken. First, check the air compressor’s RPM to see if it matches or is lower than what is recommended by the manufacturer. Next, clean and lubricate all bearings on the engine with something designed for this purpose before running an oil analysis test to determine whether any other maintenance needs to occur.
If you have exhausted these options, installing higher-performance parts may be necessary to get more power from your air compressor. As discussed earlier, increasing CFM will lead to better performance and fuel efficiency, leading to our next point – decreasing operating costs! We hope this blog post was helpful enough to understand how to increase Cfm on the air compressors. Feel free to reach out to us if you have any questions to ask.