How to Fix Crazing in Pottery
Whereas potters could be quite artistic and imaginative, they could even learn lots of anything from the industrial sector whenever it comes to handling the craziness. Firstly, you can’t neglect the problems linked with cleanliness and hygiene and capacity. The next is that an item does not look insane out of the furnace, it can also be a very weak glaze match, and it can only be a matter of how long it appears.
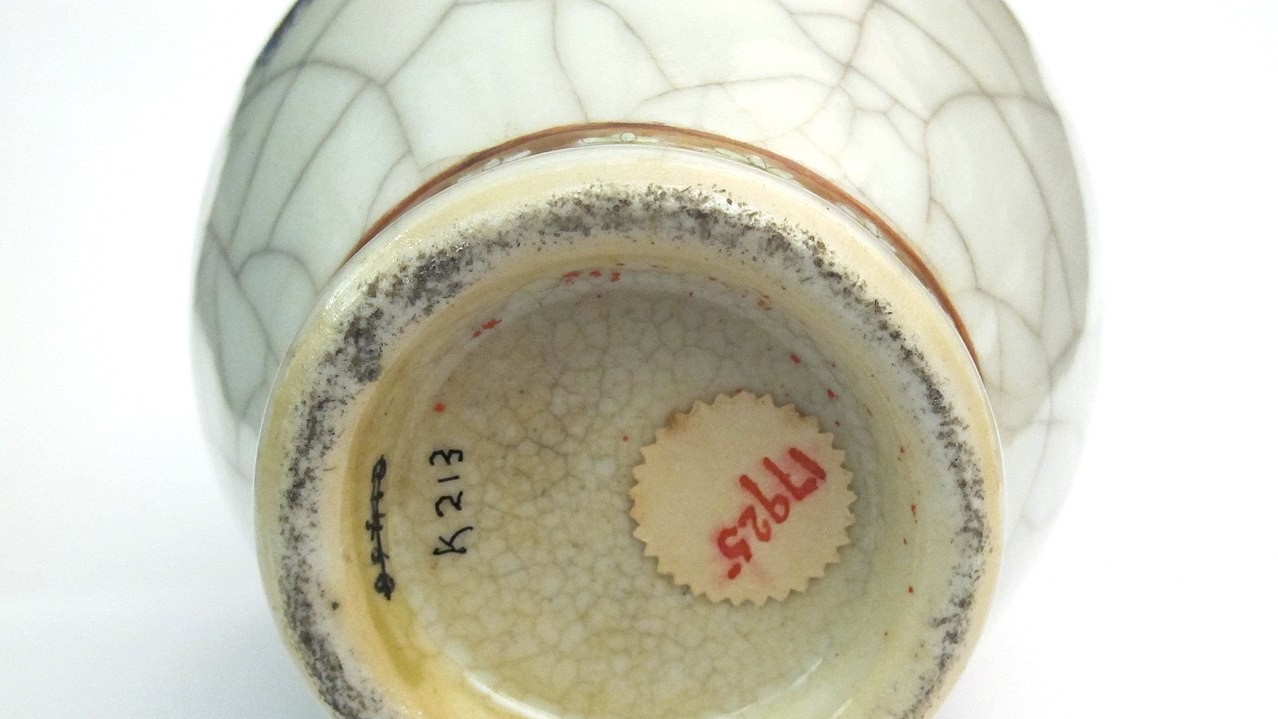
Because glaze and mud are attached, they should become consistent with extension, so no quantity of ‘covering over’ this inconsistency can render it vanish. At all, Band-Aid solutions buffer the period before crazing begins. The only proper fix is to modify internally or glaze enlargement, or even both. When a given remedy does not accommodate that, otherwise, you handle the effects and not the source.
The presence of crazing in center-fire and elevated-fire where glaze and design construction is finer, indicates a significant inconsistency, not a minor problem. Crazing is partly related to misalignment among the body and sprinkle on the temperature change. It stretches and decreases when a part of the ware is exposed to heat throughout daily usage.
An inconsistent mud and glaze generally indicate the glaze falls by shivering, either instantly or gradually (the latter is most popular). Tests were conducted have shown up to a triple distinction in the toughness of glaze sample bars among elevated / lower growth variants of a glaze with no noticeable craziness to recommend an issue.

This implies that there are already unfinished causes of stress, which leads to a massive point of toughness by the time when crazy comes back. Significant reform is required to repair it, something that not just fixes repairing the crazy trend but also returns the clay/glaze ‘love’ ignited energy.
The amount of glaze and the structure of the body are determined by the amount of oxygen. This means that any repairs need to involve checking the body and the glaze chemistry.
Implement a Narrower Layer of Glaze
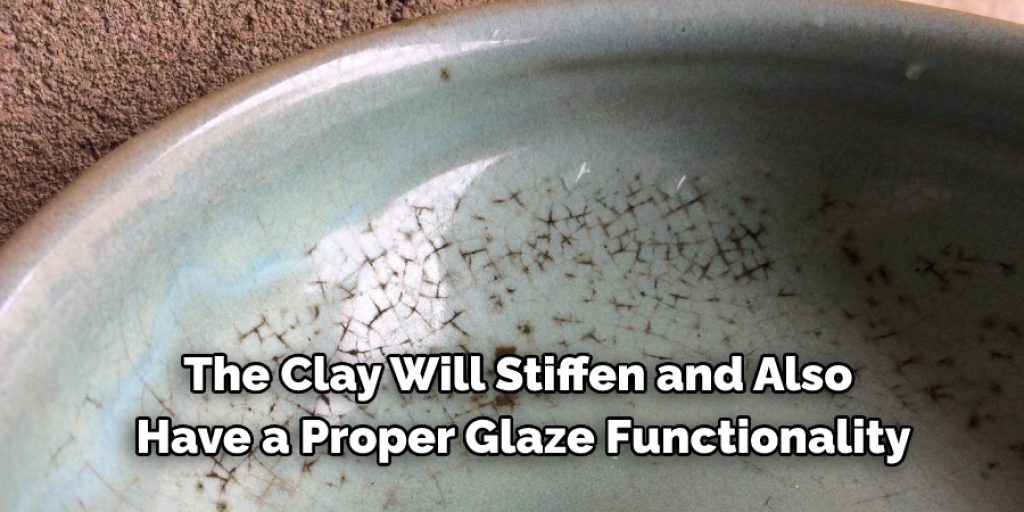
Of course, this is not best to opt a sure amazingly-thick responsive glaze, but if that doesn’t accommodate certain ordinary film thickness, it’s doesn’t match in. This can craze any time it happens added too dense.
Erase Several Other Feldspars and Silica Added Line Mixture
The feldspar may produce the problematic elevated-expansion oxides of K2O and Na2O, but if you extract those glazes will not settle sufficiently (unless it has been over-melted beforehand, of course).
Higher or More Extended Burning Period
One statement is that the clay will stiffen and also have a proper glaze functionality; this more robust operating system will make alignment well. With a crazy glaze, a great design doesn’t indicate a better match; it implies a pressured match.
Attach Even More Significant Concentrations of Silica
Sure, sometimes, in instances of tiny bit crazing, it might operate where gloss can accept the most silica. But incorporating sufficient to cover out-of-the-kiln crazing merely does not solve the broader fitting issues. The internal pressures between the structure and a higher flow glaze could distort the ware and inevitably craze it anyway.
Apply 5 Percent Silica Amounts to the Heated Surface
If you want to change the skin of your clay project, you will need to use a different type of clay. However, if you are using a formulated clay, it is not possible to change the skin. If you want to change the skin, you will need to use a coarser size and shape of elevated-expansion silica. This will compact the glaze and make it more difficult to change the skin.
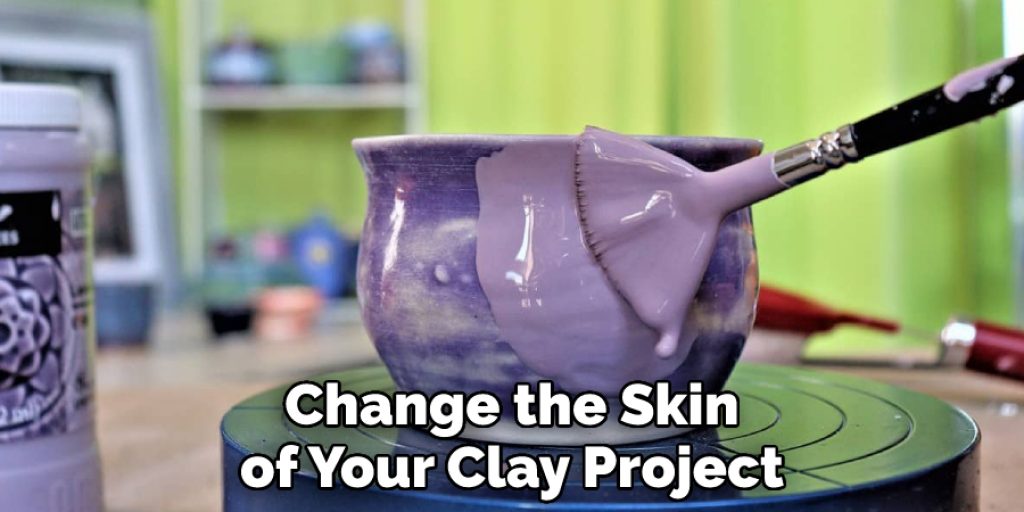
Cool the Glaze Furnace Slowly, Do Not Launch That Till Under 200 ° C
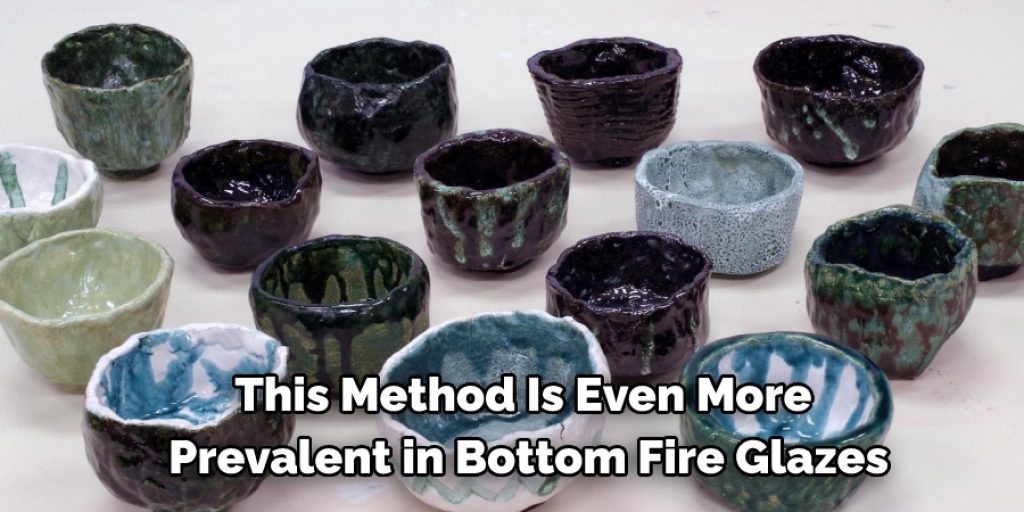
When could the glaze even only endure a nice regular period after burning, now how will it handle the dish washer’s heat abuse or the daily hot-cold surprises of daily usages? This is likely that whenever the furnace is released, a glaze in pressure will be relaxed off, which might well seem OK. And the first heat input she initiates in use will uncover what is momentarily hidden from view by the smooth cool.
Alter to a Lower-Expanding Frit
This idea is going in the right way because it is recommending to modify the enlargement. Nevertheless, fewer frits have been used in glazes made of stone (the ones usually there for a particular reason). So merely moving to a frit with specific chemistry and smaller expanding would entail changed glaze qualities unless you realize the consequences. This method is even more prevalent in bottom fire glazes as many boron frits are very structured by themselves, nearly stand-alone glazes.
Bisque More When Lower Thermal Glaze Doesn’t Match
This is more challenging to have a glazed work on a lower temperature body in which there is a shortage of clay-glass control. Band-Aid strategies did not work; the clay and glaze temperature increases have to resemble closely. This is possible that reduced-fire crazing can be apparent, but a far narrower gap between extensions of clay and glaze than for stoneware. Therefore minor variations have a more substantial impact.
Tips to Prevent Crazing in Pottery:
1. Keep the kiln at a lower temperature when using glazes that are not compatible with each other.
2. Do not increase the bisque temperature over 1400 F before glazing. If your pottery was glazed without being fired to maturity, there is a higher chance of crazing after being fired for the first time.
3. Do not place a glaze over another glaze fired to a temperature below its compatibility range.
4. Be sure to have the correct glazes in your kiln before firing to adjust your bisque temperature accordingly.
5. Apply a glaze in a thin layer rather than thickly.
6. When stacking bisqued pottery, do not solder or apply lead came between pieces that are prone to developing crazing lines.
7. When stacking pottery pieces after applying the glaze, be sure to leave enough space between them so that firing heat can reach all areas of the piece.
8. Allow your ware to cool slowly, do not drop it into water or quench it in oil or brine. This can cause severe cracking that makes worse any crazing lines.
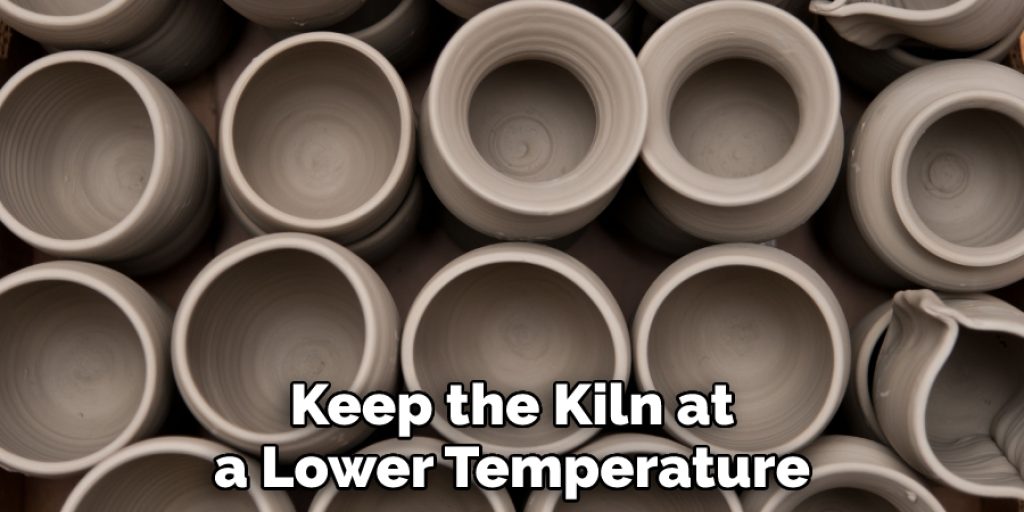
How Long Does it Take to Fix Crazing in Pottery?
The short answer is it depends. It’s largely a function of the depth of the crazing (the length of the cracks), whether more than one thickness of glaze is involved, and what the pattern of crazing is (i.e., whether it’s random or runs in a diagonal line).
We usually tell people that if we can inspect and repair all the crazing on a glazed surface within an hour, it will not cost more than $75.
If the repairs are hidden, there are no limits on how long it can take to fix crazing in pottery. Repair time increases directly with the amount of effort involved. The more extensive the repairs, then the more likely it is that additional surface grinding or surface glazing will be needed to blend the newly repaired area into the surrounding unbroken glaze surface.
Frequently Asked Questions
What Causes Crazing Pottery?
Crazing is the result of internal stresses and microcracks. This is a term that describes a condition where pieces of pottery are cracked by stress or expansion, usually as a result of uneven shrinkage during firing.
This can be caused by using different glazes on the same piece, using thin-walled clay pots with skinny walls, or stacking pots too close together in storage.
Is Crazing in Pottery Bad?
The crazing in pottery is a natural phenomenon that happens when the clay reacts with water and air. The crazing process happens when different minerals are exposed to water, which creates beautiful patterns and textures.
Crazing can be seen as a defect in the finished product, but it is actually not bad for your pottery.
What Makes Pottery Shiny?
Pottery is typically made of clay, which has a high silica content. This makes it shiny when it is exposed to the sun’s rays or another source of heat.
Pottery can also be glazed with either a lead-based paint or an enamel coating that contains lead. These coatings are considered harmful if they chip off and enter the food chain through erosion and digestion, so they should not be used on dishes intended for human consumption.
What Are Tiny Cracks in the Glaze of Pottery?
A change in the firing temperature can cause tiny cracks in the glaze of pottery. The difference between the high and low temperatures can also cause tiny bubbles to form on the surface of the glaze, which can then lead to cracks.s.
The most common type of crack is called “blowout” because it resembles an explosion where a hole appears on one side of the piece. Other types include:
• Gaps: This occurs when too much heat is applied to the ceramic ware during firing and causes portions of ceramic pieces to fuse, leaving behind gaps or openings within the piece.
• Hemlines: These occur when unevenness in thickness or density causes some parts of a piece to cool faster than others, resulting in a break along these lines.
Can You Glaze Pottery Without a Kiln?
A kiln is a device used to heat air or other gases at high temperatures and slow down the cooling rate so that objects can be fired in it.
The first step to glazing pottery without a kiln is to ensure you have everything needed for the project. The most important item needed is a clay body that has been prepared for glazing. This includes:
• Cleaning the piece, removing defects such as cracks, particles, and bubbles.
• Adding colorants like slips and stains if desired.
• A firing schedule that ensures the piece will withstand fire temperatures over time without cracking or shattering.
• A graphite or other binder material added into the mix if desired.
Conclusion:
Crazing is cracking that often appears on pottery. Various factors can cause it, but there are ways to fix it if you catch it early. In this post, we have explored what crazing is, the causes and effects, and how to fix it if your pottery has been affected. If your pottery has started to develop crazing, you can do a few things on how to fix crazing in pottery.
However, if the crazing is too severe or widespread, it may be best to discard the piece and start again. With a little bit of effort, though, you should be able to restore your pottery to its former glory. Have you ever had to deal with crazing in your pottery? What methods did you use to fix it? Let s know in the comments below!