How to Measure Dust in the Workplace
Dust can cause a variety of respiratory problems and allergies, as well as other potential health issues. Unfortunately, many people are unaware of the way to measure dust particles in your work environment. If you do this, you can make sure that everyone is safe.
This blog post will outline some ways for you or your employees how to measure dust in the workplace so they can take necessary precautions.
The amount of dust in an indoor environment depends on various factors, including ventilation rates and the type of building material used for construction which affects how quickly dirt is deposited on the surfaces of the building. Read on to know more information.
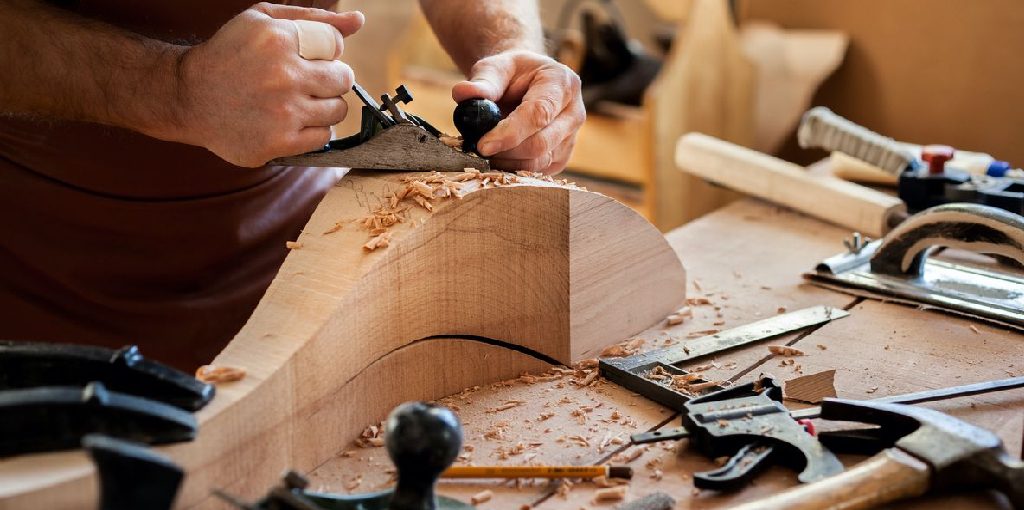
Five Reasons Why You Should Measure Dust in the Workplace:
1. Numerous worker complaints have shown that dust is a respiratory hazard. Symptoms of health problems can range from mild irritation to chronic bronchitis, asthma, hypersensitivity pneumonitis, fibrosis, and even disabling central nervous system disorders.
2. Inhalation exposure to particles smaller than 10 microns in diameter has been associated with cancer in animals and humans.
3. It is believed that the vast majority of particles taken into the worker’s lungs are deposited there rather than exhaled.
4. Also, it is widely recognized among doctors and scientists that small particle size is more hazardous than larger particles because smaller particles are closer to the gas exchange region of the lung where oxygen enters the body.
5. The most recent studies indicate that at least some ultra-fine particles are more hazardous than small particles because they have a greater surface area per unit mass.
10 Ways on How to Measure dust in the Workplace:
1. Digital Image Analysis:
This is a great way to measure dust in the workplace. You can use it for delicate work like this or coarse material found in the paint industry. This process uses digital image analysis to find particle sizes and concentrations.
2. Tape Test:
First, place a piece of tape on a surface, and then use adhesive tape to attach the sticky side to the tested object. Once this is done, pull off the adhesive tape from the surface and press that side against a microscope slide. Use what is called a “microscope cassette” or “micro cassettes” with a clear base.
3. Gravimetric Method:
This is a method for measuring the weight of dust. This method’s advantage is that it accurately measures total dust concentration in the air. It uses a balance of scale and water-soluble glue. You can also use sticky tape to collect particles on many types of surfaces before weighing the sample.
4. Airborne dust concentrations:
This method uses the weight of the solid collected on an air filter or surface to measure airborne dust concentrations. You can place air filters in a cleanroom or other location where you want to monitor dust concentration.
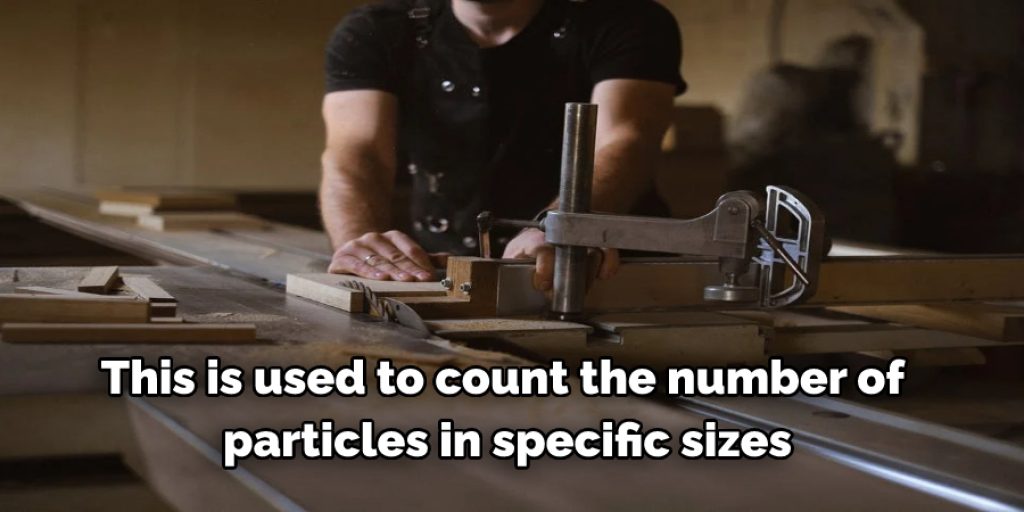
5. Filter Counts:
This is used to count the number of particles in specific sizes. It can be used to determine if there are any harmful dust concentrations in an area, but only if the proper instruments are used. This method uses filters that capture airborne particles onto the adhesive tape. The tape is then transferred to a slide and allowed to dry. A microscope is used to count the particles on the filter.
6. Bubble Counting:
This method uses a bubble counter that helps track the number of airborne particles. These bubbles are sized based on their ability to pass through a defined aperture, which helps determine particle diameter. This method is used to measure particles in any size range.
7. Lab Analysis Results:
You can use lab analysis results to determine the amount of dust in an area or recognize an airborne dust problem. You must use the correct units to compare lab results with the units of your measurements to have a proper comparison.
8. Relative Density (specific gravity):
This method can be used to determine the total weight of dust in a given volume of air. This method is generally used to measure low particle concentrations where other methods are not applicable or practical. It requires collecting samples onto filters, weighing them, and calculating the mass per unit volume.
9. Coarse Particles:
This method measures particles too large for other ways but not large enough to be considered dust. It’s necessary to use a microscope with high magnification, a light source, and an area outside the light path for viewing. This way, you can see how much dust is.
10. Diamter Separation Method:
This method is also known as particle size distribution or PSD collection efficiency. It measures the intake capacity of your intake system by measuring the geometric mean diameter (GMD) of particles you are trying to collect.
5 Common Mistakes to Avoid When Measuring Dust:
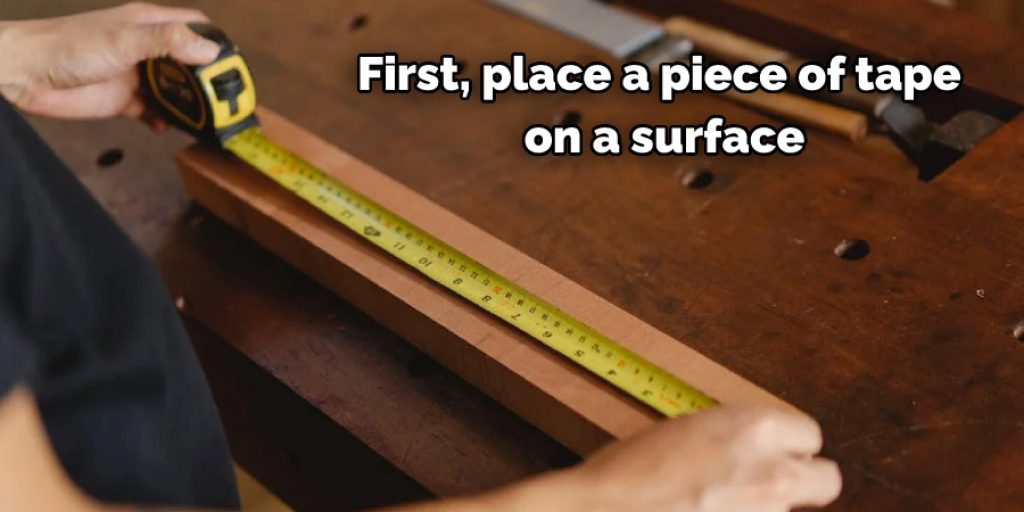
1. Relying on a Particle Counter to Measure All Dusty Areas:
While it’s true that particle counter technology is well-suited for measuring particles in the air, this technique is insufficient for measuring dusty areas.
2. Using the Wrong Measuring Device:
Dust particles vary in size, and different particle counters are designed to measure specific dust sizes.
3. Not Adjusting the Particle Counter’s Settings for Local Conditions:
Each environment presents its challenges for particle sizing. For example, what looks like a 0.5-µm particle to the naked eye might measure between 1.0 and 1.2 µm depending on whether it’s indoors or outdoors, day or night.
4. Thinking of All Dust as Equal:
Not all dust particles are created equal. For example, particles found in sawdust are quite different than those found in lead paint chips or asbestos fibers.
5. Turning Off the Particle Counter:
A particle counter is only useful if it’s turned on and ready to go when needed. If a particle counter isn’t being used or is in sleep mode, it will greatly diminish its ability to detect particles.
Conclusion:
To effectively measure the level of dust in a workplace, you need to understand how much dust is being generated. You can then calculate the average amount per hour and use this data as a baseline for your future tests. In addition, it’s essential to know what type of particle is present and where it originates from so that appropriate preventive measures can be taken.
For example, cleaning agents or filters may help reduce airborne particulate matter if they are identified as coming from specific sources like ventilation systems or other on-site machines.
Finally, take measurements of the amount of dust before any work was done to compare it against all our hard work! We hope this blog post on how to measure dust in the workplace helped you understand the different concepts of measuring dust.