How to Make Porcelain Clay Figures
Porcelain clay is a clay structure which, due to its bright yellow texture, lightness, and the manner surfaces gaze so fantastic on it, pulls numerous potters. However, it’s a clingy tiny clay structure that can collapse during the process of developing (particularly on the pottery wheel) and change direction all through firing.
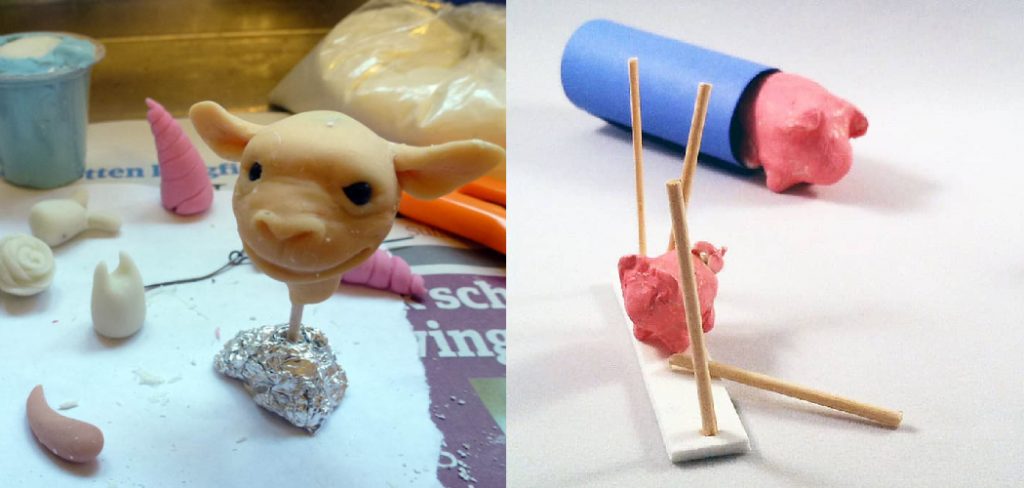
That’s why so many starting ceramics courses start again with a considerate clay body, like stoneware clay. Cold porcelain mix is also mixed with additives to attempt to prolong the shelf life of its function and to guarantee that it does not deform. Under normal domestic conditions, the compound should usually survive at a minimum of 1 week without preservatives when the substance is tightly packaged.
Witch hazel, lemon extract, citric acid dust, or clove oil are additives which could be helpful in preparations. Have used is sodium benzoate, and also some previous ingredients involve formalin/formaldehyde, which must be prevented because it is harmful to health. Verify for the thickener additives before you buy quality porcelain clay blends!
But it is so beautiful that I want to reconsider my position with it, for one. You will know how to cooperate with persnickety porcelain mud with training and reduce the failure risk. Gwendolyn Yoppolo discusses what porcelain clay can hold up to from the damp to the bone dry process. It is a non-toxic, clean and easy to work with clay that is incredibly versatile for anyone who doesn’t have the time or space to make their own porcelain.
Enhance Your Porcelain Clay Performance
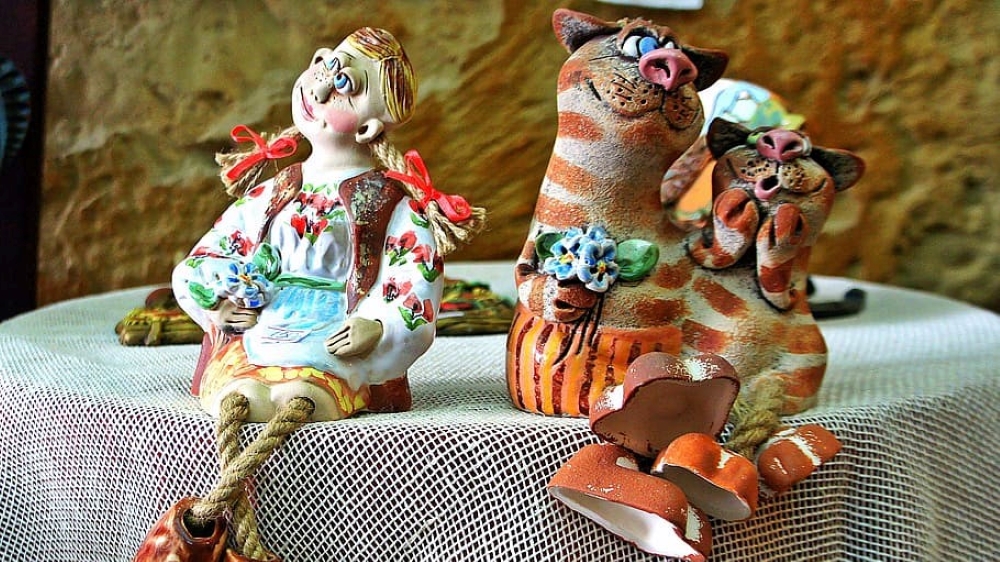
Porcelain directs us to be observant and reliable in our contact. Further than the fundamental performance aspects that clay body parts both have in widespread, porcelain clay also does need to be viewed to prevent twisting and to clamp all through rinsing and burning. Learning the pacing is among the most critical aspects to remember – it’s only taught by practice.
Porcelain Clay: the Timing Is All There!
When you pursue such timing strategies for porcelain, these will certainly enhance your performance! Adding into a very fragile shape creates a drop. You are using softer clay to a very sharp mold crease splitting. Modifying and flexing a too dry or leather-hard form induces warpage and breakage. Now you understand how to fire ceramics, let’s get into the basics of how to glaze pottery. Glazing is a vitally important aspect of the firing process.
In stock, attach parts with equal drying and stabilize both joints with additional clay and compact them along with an arm. Compression, more compression! Smooth, and even drying is crucial so if drying clay sculpting, particularly with porcelain clay. If the clay is somewhat dry you may have the ability to reattach and dry it. Sculpting time, the clay is a little bit dry.
Pause times, when the parts are enclosed in a sealed environment for gradual drying and moisture transfer, also aid. At every step, the clay can become used to its new style, without getting one portion dry too fast for the entire piece. A further important method is restricting part motion during the drying process. Any internal stresses in the clay will lead to drying crack formation. This can be achieved by gluing the piece together with a temporary adhesive, or using tape on the outside of the part.
Here’s just a vague outline and timetable on when to do something in porcelain while operating. The steps are not different but are divided for comparison purposes from the framework of the full course. In reality, they mix in several ways, particularly the “cheese” parts. Even if porcelain is thixotropic, after it has attained the hard cheese step, this has a lovely way to resort, so that you can start going back and execute several other soft cheese procedures.
For a point, porcelain clay even rehydrates nearby, and you can go away into a localized region. Such guides are intended to provide you with a reference point for working out your method of achieving performance. In an effort to achieve high performance, businesses that run highly active internet sites set up server-side software and distributed networks of servers. The former provide in depth management and production control over the entire system.
Related Article: