How Are Metal Straws Made
Introduction:
Metal straws are cylindrical tubes made of stainless steel, aluminum, or another alloy. They come in various weights and diameters and can be bent to suit an individual’s needs. Today, they’re gaining popularity worldwide for their versatility and eco-factor.
Whether you prefer cold or room temperature drinks, metal drinking straws allow you to travel with your drink without fear of breaking glass or spilling iced tea all over yourself. In this article, I will discuss how metal straws are made. So let us get started.
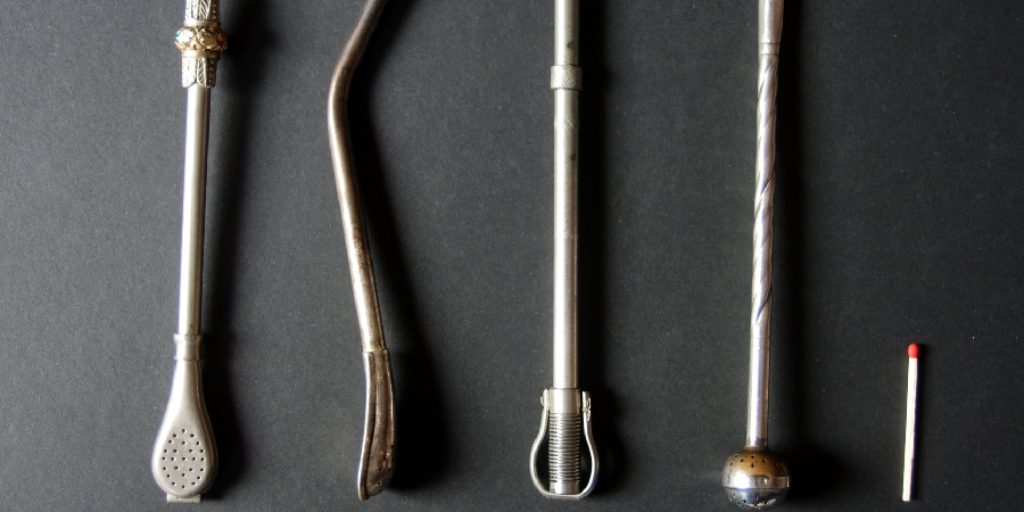
A Detailed Stepwise Guide on How Are Metal Straws Made:
Material used:
Stainless steel is the most common material for constructing metal straws, although aluminum and other alloys can also be used. The most suitable of these materials will depend on the intended purpose of the straws in question.
For example, a thin-walled alloy such as aluminum may be more comfortable for children to use than a thicker-walled stainless steel option.
Step 1: Extrusion:
In this step, a metal tube is extruded into a cylinder that forms the body of the straw. Sometimes, the tube is spun into its final shape, producing a hollow cylinder with slanted or cut edges at one or both ends.
Step 2: Pressing and bending:
In this step, the metal straw is pressed through a die to give it its final shape. This process will result in one flat side at each end of the cylinder (this feature helps prevent drinks from leaking down the sides of the straw).
This stage also involves bending or crimping either end so that they meet at an angle. Sometimes, the edges may be slightly flared to provide a comfortable feel when drinking. It should be noted that alternative shaping methods such as spinning and swaging could also apply in certain circumstances.
Depending on how much work is desired from the finished product, these can involve even more complex pressings and heat treatments involving different metals.
For example, different materials can be used at each end or along the length of a metal straw to provide an easy grip. However, this approach requires more effort and usually makes the finished product less cost-effective.
Step 3: Cutting to the final length:
In many cases, this step is required before other processes can begin. The cutter will consider any additional features that have been added in previous stages when determining the appropriate position for cutting.
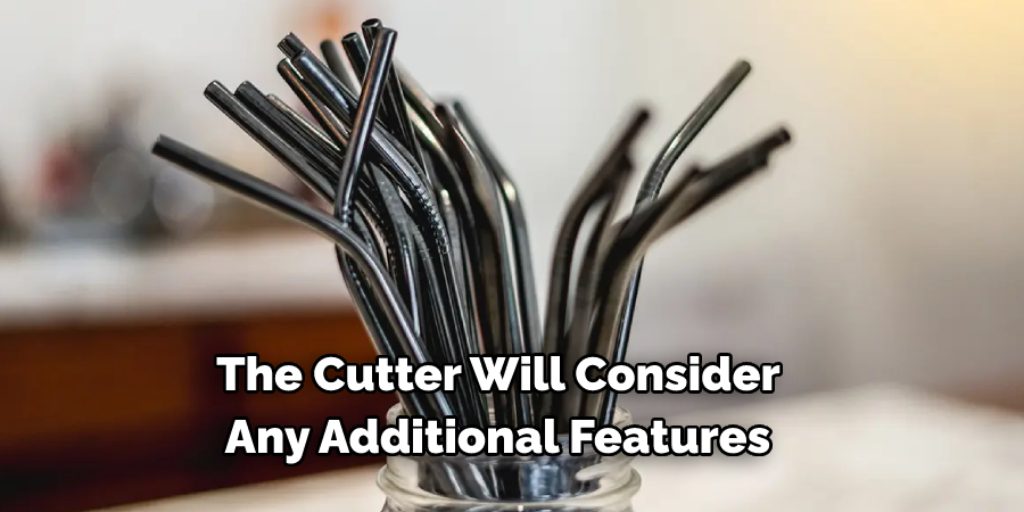
For example, if a flared edge has been incorporated before this stage, it should be cut to appear outside after completion. This helps ensure that drinks can travel all the way down, into the straw without spilling over one or both ends. It also makes it easier to drink from the straw as there is less chance of creating a vacuum.
Step 4: Polishing and cleaning:
This step will depend on the requirements of those who will be using the resulting straws. For example, if they are intended for commercial use and require an attractive finish, they may pass through a manual cleaning process and receive an additional polishing treatment.
If this approach isn’t desired, it can be omitted completely or replaced with other processes such as brushing or sanding. In some cases, a surface coating such as plastic or even gold may be applied to the metal straws after polishing.
This can increase their durability and provide additional properties that make them more amenable to commercial use. For example, it may enable customers to choose from a wider range of colors to personalize their straws.
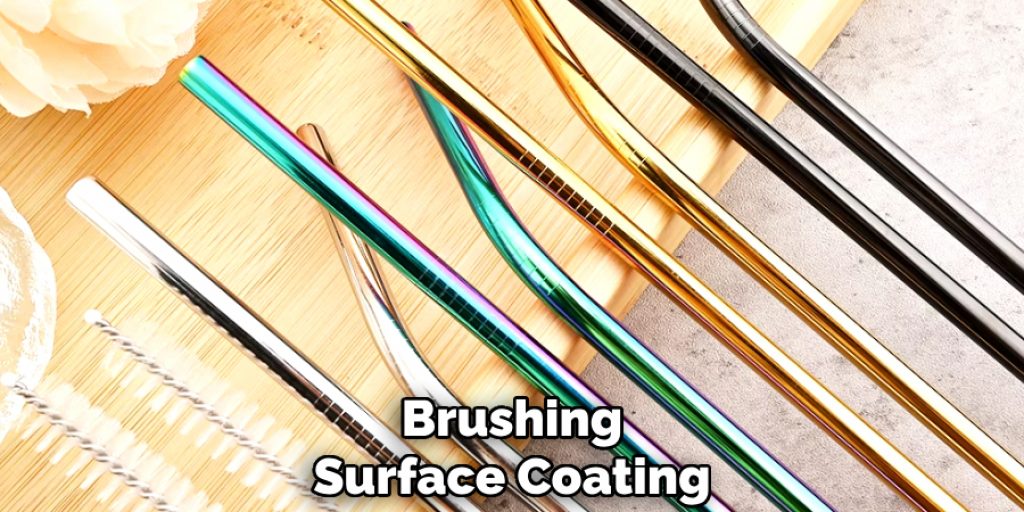
Step 5: Packaging:
Packaging – Your metal drinking straw is now complete! Do you know how metal straws are made? You might think, “Hey, I am done.” But actually not yet. Because you have one final task before you put your product on the shelf for sale – packaging!
Packaging is essential for all types of products because it tells everyone about your brand and makes it more awesome. Packaging also acts as a protective barrier and prevents damage to the product during transport and storage. Packaging, therefore, serves many purposes.
The type of packaging needed for straws depends on the material they are made from. For example, if they are made from plastics or glass, simple paper wrapping may suffice to protect them adequately until they reach their final destination.
However, metal straws require stronger protection than this since they can sometimes become twisted and bent during transit which can cause leakage of drinks inside the package. Wrapping them individually into separate plastic packets is one way that this problem can be circumvented if necessary.
Precautions While Making Metal Straws:
Some precautions need to be taken care of before making metal straws. These include:
1) While working with a saw, wear goggles and a mask to protect the eyes from flying pieces of metal. Also, wear clothes that cover your mouth and nose. This way, you can not only stay out of harm’s way but also prevent contaminants from entering your body through breathing in dust particles.
Gloves should also be worn and earplugs if necessary to avoid noise-related injuries. If you are working with a drill or other handheld device, ensure it is powerful enough for the task at hand without being underpowered or dangerous simply because it doesn’t have enough power. Finally, ensure proper ventilation when cutting large amounts of sheet metal.
2) When soldering, use Mapp gas or propane, which are less hazardous than the normal butane lighter for heating metal pieces together. However, always be careful with the flame and never touch it to any part of your body, as even a momentary contact can result in severe burns.
If you do not have access to this type of fuel, you will need some lubricant on hand, such as beeswax, to ensure that the metal pieces slide smoothly past each other when fused. Work quickly so that the solder does not begin to harden before the joint is complete.
Also, make sure that you clean off dirt or impurities from both pieces of metal before beginning to solder them; otherwise, moisture may cause the solder to run and spoil any clean lines you try to create.
3) When filing or sanding, be sure to work carefully and methodically. Both actions can result in injuries such as cuts from broken pieces of metal flying off unexpectedly at high speeds.
Make sure your work area is safe for this activity. No one else should be allowed in until the area has been thoroughly checked for sharp debris and other tools that could cause injury. Also, wear eye protection when filing or sanding to protect your eyes from harmful dust particles.
You Can Check It Out to: Solder Metal Crafts for Art
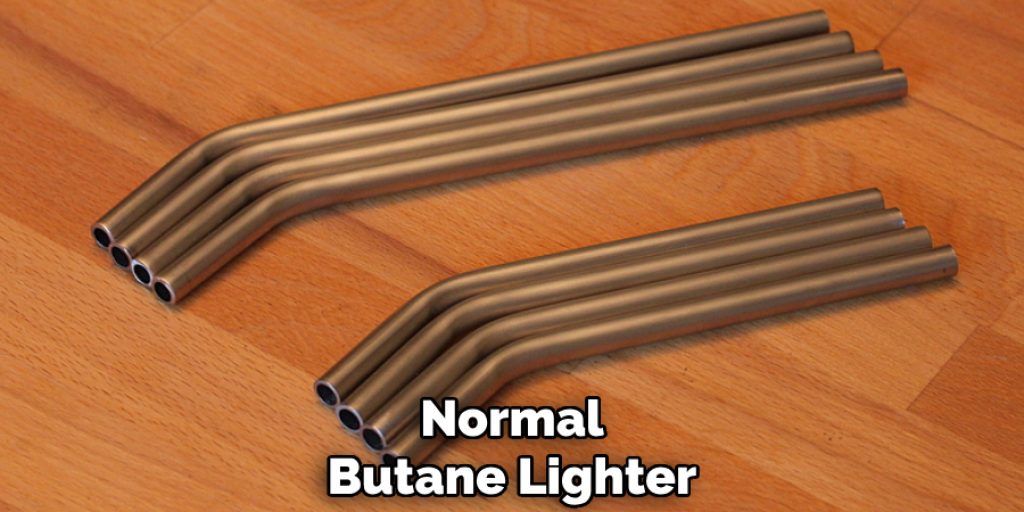
Conclusion:
I hope this article has helped learn how are metal straws made. Ensure precautions while performing the process. Thank you and have a nice day!